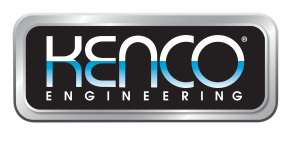
Kenco Engineering is a key supplier of instrumentation for oil & gas, petrochemical, power, pulp and paper, water and waste treatment.
Kenco is a leader with liquid level gauges, oil level controllers, sight flow indicator, chemical process equipment, engine and gas compressor equipment. Kenco’s oil level controllers are the worldwide standard for measuring and controlling the amount of lube oil consumed in stationary engines and compressors.
Chemical Injection Quills
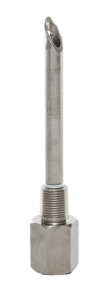
Features: Kenco chemical injectors are designed to inject and properly atomize corrosive chemicals into the turbulent stream of a process system pipeline. The Kenco chemical injector will minimize the possibility of corrosive chemical build-up on the walls of the pipeline.
• Patented aspirator tip design on injector disperses chemical evenly into process stream and away from pipe walls
• Check valve in injector eliminates backflow
• Injector is ideal for high pressure applications up to 6000 psig
• Injector has been designed so that it can be mounted in any orientation
• Standard insertion lengths available up to 24” long. Custom sizes also available.
• Injector available in 316 Stainless Steel, Hastelloy C-276, and CPVC
Day Tanks + Stands
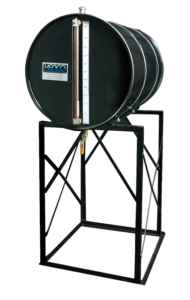
Features: The KENCO Oil Supply Tank & Stand System is designed to supply lube oil to the crank case of a compressor or engine in an isolated location where daily supervision and maintenance are an impossibility. KENCO Oil Supply Tank & Stand Systems used in conjunction with our oil level controllers with low level switches can provide 24 hour protection from lubrication failure. Oil Supply Tanks are available in 5, 16, 30 and 55 gallon capacities.
16G-36 = 16 Gallon Tank with 36″ Stand
16G-56 = 16 Gallon Tank with 56″ Stand
16G-72 = 16 Gallon Tank with 72″ Stand
36S-16 = 36″ Stand for 16 Gallon Tank
56S-16 = 56″ Stand for 16 Gallon Tank
72S-16 = 72″ Stand for 16 Gallon Tank
Draw Down Cylinders
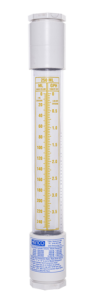
Features: Kenco Draw Down Calibraion Cylinders are used for these applications:
• To calibrate the flow rate of chemical metering pumps and chemical injection systems
• To periodically monitor the performance and accuracy of a chemical injection system
• To insert accurate dosages of chemical into batch processes
Dual Scale:
Total gauge volume in millimeters
Gallons per Hour or Liters per Hour scale for a one minute test of calibration to determine flow rate
Mylar laminated scales are protected from attack by harsh chemicals
Available in capacities ranging from 60 ML up to 10,000 ML
Models with threaded NPT connections on both ends or models with removable slip-on top caps available
Rugged construction using transparent PVC pipe and industrial grade PVC fittings
Sight tube material is clear and impact resistant superior grade PVC
Materials of construction are qualified to handle a wide range of chemicals
Lightweight and extremely easy to handle
Special sizes available upon request
Other materials also available
Flow Indicators
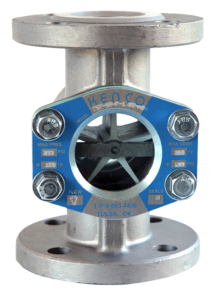
Features: KENCO Engineering Company offers a variety of Standard KSF (cast body), Full-view, and Armored Sight Flow Indicators, as well as, a line of Sight Windows. All products are hydrostatically tested to ensure reliability in harsh operating conditions. KENCO Sight Flow Indicators provide a window into piping.
KSF= Cast Body Sight Flow Indicator
HT=High Temp. / High Pressure
F=Flanged (150#)
2.0=2”
P=High Temp. PTFE
S=316 Stainless Steel
R=Rotor (1/4” to 4” Sizes Only)
Level + Rate Gauges
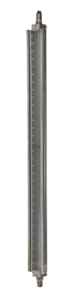
Features: The 5700 Series Gauge provides a visual means for checking the contents of a bulk tank and a means for checking the injection rate of a chemical metering pump. The gauge is designed to operate in low to medium pressure applications up to 500 psig.
The 5700 series has 1/2” MNPT x 3/8” FNPT threaded process connections. 1/2” to 2” flanged process connections are also available. The standard sight tube is 5/8” O.D. glass. Other sight tube options are also available upon request. The 17000 gauge is fitted with 1” MNPT process connections (flanged process connections are also available). The standard sight tube is 1” O.D. glass, which makes it ideal for viscous liquids.
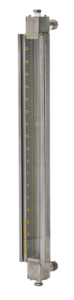
Features: The 8800 Series Level Gauge features 90° connections for ease of installation. The Gauge is fitted with inline 1/4” FNPT vent and drain connections. Vent and drain connections are inline for routine maintenance of the level gauge. The centerline dimensional tolerance is ± 1/16”. This assures that the gauge will fit the mounting connection of the tank.
The gauge frame is available in carbon steel or 304 stainless steel. A wide variety of wetted materials are available, including carbon steel, 316 stainless steel, alloy 20, Hastelloy C-276, PVC, CPVC, Kynar, and high density polyethylene.
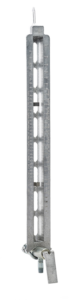
Features: The 929 Series Pump Setting Gauge provides a means for checking the pumping rate of any chemical pump under actual pumping conditions in one minute. The gauge mounts in the pump’s suction line between the reservoir tank and the pump. It provides a visual gauge showing the liquid level in the reservoir in addition to a rapid means for setting the pump. The maximum pump rate for the 929 Series is 45 Quarts per Day or 42.59 Liters per Day, with each mark on the scale representing 1 Quart/1 Liter per 24 hours. Models are available with a coupler plug so that the unit can be easily disconnected for calibrating several chemical pumps.
13″ Cast Aluminum Frame
No Test Valve
Wetted Parts 303 Stainless Steel, Aflas O-Ring Seals and Glass
1/4″ MNPT Mounting Thread
1/4″ FNPT Vent
Polycarbonate Metric Rate/Height Shield
Each Division is Pump Rate of 1 Ltr/24 Hrs.
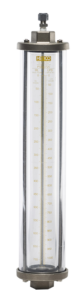
Features: The KENCO Accu-Rate Pump Setting Gauge® utilizes precision scientific glass to provide the most accurate reading possible for calibrating the flow rate of a chemical metering pump. They are also used to periodically monitor the performance and accuracy of a chemical injection system. Additionally, the Accu-Rate Pump Setting Gauge® can be used as the primary containment reservoir of a fluid that will be pumped into a chemical injection system.
Precision borosilicate glass sight tube delivers precise rate calibration from 0.05% to 0.2%
Accu-Rate Pump Setting Gauge® will calibrate pump rates up to 1095 gallons per day and 4140 liters per day. Clear polycarbonate shield for impact resistance is standard on all models.
Five (5) scale options are available: U.S. gallons by volume (USG), gallons per day (GPD), gallons per hour (GPH), Liters per day (LPD) and Liters per hour (LPH) – Standard volumetric scale in ML on all units.
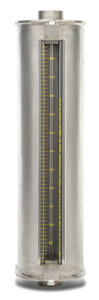
Features: Calibration Pots provide an accurate pump Calibration of higher pump flow rates. The totally enclosed construction assures maximum safety. The Gauge is installed between the suction side of the Chemical pump and the Tank. The Pump rate is checked by closing the Valve between the tank and gauge and observing the level change in the gauge for one minute.
Design utilizes a tank with Shielded tubular gauge for maximum protection from glass breakage. Provide a means for accurately checking the feed rates of a chemical metering pump. Manufactured in PVC, Carbon Steel and 316 Stainless Steel as standard materials. Can provide other materials to meet any chemical resistance requirements. Individually hand calibrated to assure maximum accuracy.
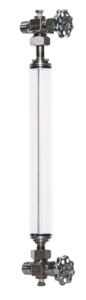
Features: The Environmental Protection Gauge (EPG) is easy to install. It installs just like tubular glass and is designed to replace your existing tubular glass. It will eliminate glass breakage and stop costly spills. The metal end connection of the gauge inserts into the valve stuffing box thus eliminating two common points for glass breakage:
Over-tightening of the glass packing
Breakage of glass at the packing nuts from impact to the gauge
Replaces unprotected tubular gauge glass.
• 360° visibility of fluid level.
• Red-line glass is standard for easy viewing of fluid level.
• The tubular valve packing nut tightens around 316 S.S. nozzles, not glass!
• Outer tube is high impact UV stabilized polycarbonate tubing.
• 316 S.S. nozzles available in a 5/8” O.D. or 3/4” O.D.
• Maximum overall length is 52 3/4”. For longer lengths, use Safeguard Level Gauge.
• Easy to install – Insert the 5/8” O.D. or 3/4” O.D. nozzles into the valves.
• Ideal for use with KENCO Tubular Valves (KTV).
Liquid Level Gauges
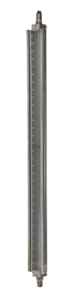
Features: The 5700 Series Gauge provides a visual means for checking the contents of a bulk tank and a means for checking the injection rate of a chemical metering pump. The gauge is designed to operate in low to medium pressure applications up to 500 psig.
The 5700 series has 1/2” MNPT x 3/8” FNPT threaded process connections. 1/2” to 2” flanged process connections are also available. The standard sight tube is 5/8” O.D. glass. Other sight tube options are also available upon request. The 17000 gauge is fitted with 1” MNPT process connections (flanged process connections are also available). The standard sight tube is 1” O.D. glass, which makes it ideal for viscous liquids.
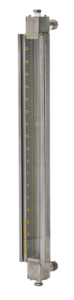
Features: The 8800 Series Level Gauge features 90° connections for ease of installation. The Gauge is fitted with inline 1/4” FNPT vent and drain connections. Vent and drain connections are inline for routine maintenance of the level gauge. The centerline dimensional tolerance is ± 1/16”. This assures that the gauge will fit the mounting connection of the tank.
The gauge frame is available in carbon steel or 304 stainless steel. A wide variety of wetted materials are available, including carbon steel, 316 stainless steel, alloy 20, Hastelloy C-276, PVC, CPVC, Kynar, and high density polyethylene.
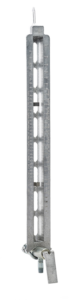
Features: The 929 Series Pump Setting Gauge provides a means for checking the pumping rate of any chemical pump under actual pumping conditions in one minute. The gauge mounts in the pump’s suction line between the reservoir tank and the pump. It provides a visual gauge showing the liquid level in the reservoir in addition to a rapid means for setting the pump. The maximum pump rate for the 929 Series is 45 Quarts per Day or 42.59 Liters per Day, with each mark on the scale representing 1 Quart/1 Liter per 24 hours. Models are available with a coupler plug so that the unit can be easily disconnected for calibrating several chemical pumps.
13″ Cast Aluminum Frame
No Test Valve
Wetted Parts 303 Stainless Steel, Aflas O-Ring Seals and Glass
1/4″ MNPT Mounting Thread
1/4″ FNPT Vent
Polycarbonate Metric Rate/Height Shield
Each Division is Pump Rate of 1 Ltr/24 Hrs.
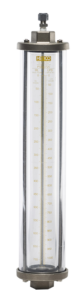
Features: The KENCO Accu-Rate Pump Setting Gauge® utilizes precision scientific glass to provide the most accurate reading possible for calibrating the flow rate of a chemical metering pump. They are also used to periodically monitor the performance and accuracy of a chemical injection system. Additionally, the Accu-Rate Pump Setting Gauge® can be used as the primary containment reservoir of a fluid that will be pumped into a chemical injection system.
Precision borosilicate glass sight tube delivers precise rate calibration from 0.05% to 0.2%
Accu-Rate Pump Setting Gauge® will calibrate pump rates up to 1095 gallons per day and 4140 liters per day. Clear polycarbonate shield for impact resistance is standard on all models.
Five (5) scale options are available: U.S. gallons by volume (USG), gallons per day (GPD), gallons per hour (GPH), Liters per day (LPD) and Liters per hour (LPH) – Standard volumetric scale in ML on all units.
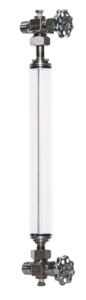
Features: The Environmental Protection Gauge (EPG) is easy to install. It installs just like tubular glass and is designed to replace your existing tubular glass. It will eliminate glass breakage and stop costly spills. The metal end connection of the gauge inserts into the valve stuffing box thus eliminating two common points for glass breakage:
Over-tightening of the glass packing
Breakage of glass at the packing nuts from impact to the gauge
Replaces unprotected tubular gauge glass.
• 360° visibility of fluid level.
• Red-line glass is standard for easy viewing of fluid level.
• The tubular valve packing nut tightens around 316 S.S. nozzles, not glass!
• Outer tube is high impact UV stabilized polycarbonate tubing.
• 316 S.S. nozzles available in a 5/8” O.D. or 3/4” O.D.
• Maximum overall length is 52 3/4”. For longer lengths, use Safeguard Level Gauge.
• Easy to install – Insert the 5/8” O.D. or 3/4” O.D. nozzles into the valves.
• Ideal for use with KENCO Tubular Valves (KTV).
Magnetic Level + Accessories
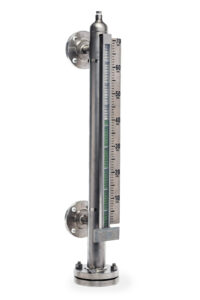
Features: The KENCO Magna-Site is a magnetic liquid level gauge used to determine the volume of liquid contained within a tank. Because the Magna-Site eliminates the need for glass, high pressure applications and hazardous locations are protected from the danger of a chemical spill due to glass failure.
The KENCO Magna-Site utilizes three major components: the gauge housing chamber, the magnetic float, and the magnetic flag assembly.
• Maximum safety – No glass is used in the construction
• Float with 360 degree magnetic flux – Maintains a strong magnetic field in all directions
• Double flag protection – Flags are hermetically sealed inside a Teflon® encapsulated assembly which is shrouded by a 300 series stainless steel enclosure on three sides with a UV-stabilized high-impact clear polycarbonate shield
• Multiple mounting options – Engineered construction allows for a variety of mounting configurations
• Compatibility – A broad range of materials can be used to withstand harsh chemicals
• Remote level indication – Explosion-proof magnetostrictive level sensor/transmitter provides a 4-20mA signal output
• Height scale – 304 stainless steel with no. 3 finish and large etched characters / lines for easy reading
• High/Low level switches – Explosion-proof switches can signal an alarm, operate a pump/valve or act as an emergency shut down
• Warranty – Three year guarantee against defects
• Reliability – KENCO has been building magnetic liquid level indicators since 1985
Oil Flow Meters + Accessories
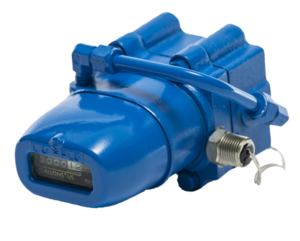
Features: The Kenco Low Flow Meter provides an accurate record of the amount of lubricating oil required to
maintain a constant oil level in the crankcase of an engine or compressor. The Kenco Low Flow Meter is a positive displacement double action, single piston meter. The piston strokes and actuates a mechanical counter that registers the amount of oil flowing through the meter. Each piston stroke equals and registers 0.01 gallon of flow. There are two models available. The model 1618 with a mechanical counter only and the model 14308 with a mechanical counter and a reed switch.
• Flow Rate Range: 0.05 to 5 gallons per hour
• Working Pressure Range: 4.6 to 50 psig
• Mechanical Counter Range: 9999.99 gallons
• Mechanical Counter Resolution: 0.01 gallon
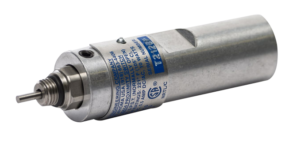
Features: The Kenco Proximity Switch provides a switch signal used to detect the absence of flow in a continuously operating compressor lubrication system by monitoring cyclic movement of the divider valve piston.
CSA NRTL/C Certified for Class I, Groups A, B, C, and D; Class II, Groups E, F, and G; Class III, Enclosure Type 4
• Switch Circuitry: S.P.S.T. (Normally Open)
• Maximum Switch Current: 0.5 Amps AC/DC
• Maximum Switch Voltage: 200 Volts AC/DC
• Maximum Switch Power: 10 Watts DC
• Maximum Temperature: 221° F
Oil Level Controller
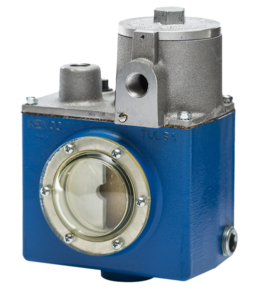
Features: KENCO Oil Level Controllers are designed to maintain the running oil level in the crankcase of stationary engines, compressors, and mechanical lubricator boxes. The KENCO oil controller works in conjunction with an overhead oil supply system which feeds the oil level controller. As the oil is consumed, the oil controller supplies the required amount of oil to maintain a proper level in the crankcase. The oil controller maintains the proper amount of oil in the crankcase using a float controlled valve. The valve opens and closes as oil is needed in the crankcase to provide a constant oil level.
Reduces maintenance by maintaining a constant lube level.
Protects against lubrication failure
Controller mechanism fully removable without draining oil
Easy view convex sight window
High pressure applications up to 70psi
Fire Safe Valves Available
Oil inlet allows for piping configuration from any direction
Oil outlets on either side of housing and in the bottom to allow for various piping configurations
Easy access to switch float through 3/8″ vent hole in top of housing for simple testing of switch operation
Direct mount adapters eliminate equalizing problems and reduce installation costs
Models available with multiple switches to measure high and low levels or low/low levels (See KHL, KSHL, KSLL)
Oil level controllers for synthetic oil applications now available
CSA & ATEX Approved explosion proof switch enclosure
Specialty Level Gauges
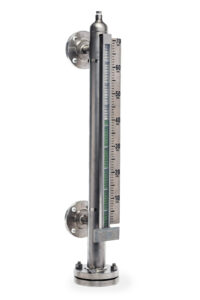
Features: The KENCO Magna-Site is a magnetic liquid level gauge used to determine the volume of liquid contained within a tank. Because the Magna-Site eliminates the need for glass, high pressure applications and hazardous locations are protected from the danger of a chemical spill due to glass failure.
The KENCO Magna-Site utilizes three major components: the gauge housing chamber, the magnetic float, and the magnetic flag assembly.
• Maximum safety – No glass is used in the construction
• Float with 360 degree magnetic flux – Maintains a strong magnetic field in all directions
• Double flag protection – Flags are hermetically sealed inside a Teflon® encapsulated assembly which is shrouded by a 300 series stainless steel enclosure on three sides with a UV-stabilized high-impact clear polycarbonate shield
• Multiple mounting options – Engineered construction allows for a variety of mounting configurations
• Compatibility – A broad range of materials can be used to withstand harsh chemicals
• Remote level indication – Explosion-proof magnetostrictive level sensor/transmitter provides a 4-20mA signal output
• Height scale – 304 stainless steel with no. 3 finish and large etched characters / lines for easy reading
• High/Low level switches – Explosion-proof switches can signal an alarm, operate a pump/valve or act as an emergency shut down
• Warranty – Three year guarantee against defects
• Reliability – KENCO has been building magnetic liquid level indicators since 1985
Switches - Flow
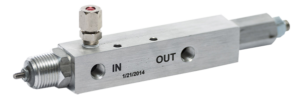
Features: The Kenco NO-FLOW SWITCH (“NFS”) is designed to protect the engine and compressor cylinder(s) against lubrication failure. The Kenco “NFS” mounts in line between the lubricator and cylinder. On start up, the first stroke of the lubricator automatically opens the “NFS” switch contact. The contact is opened and closed by the precision-fit plunger inside the “NFS” body. Lubricator oil flows through the body with the rate of flow controlled by the amount of oil that passes between the precision-fit plunger and the bore inside the body. If the lubricator stops pumping, the precision-fit plunger will drift back against the switch contact and stop the engine.
Switch Contact Electrical Rating: 2 amps, 30 VAC or VDC
Switch Contact Circuitry: Case-To-Ground
Flow Rates Required to Open Switch Contact:
• 6 drops per minute or more when using standard plunger spring
• Between 3 and 6 drops per minute when using optional light plunger spring “L” (See ordering note below)
Maximum Recommended Working Pressures:
• NFS-3, NFS-4, NFS-5, NFS-30: 2,000 psig
• NFS-6, NFS-11: 4,000 psig
• NFS-7, NFS-9, NFS-25: 1,750 psig (Consult factory for other available rupture pressure settings)
Switches - Level
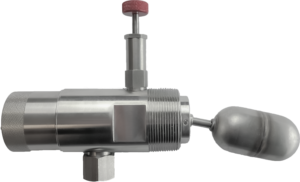
Features: The Model KEFS uses a float to determine the presence or absence of liquid in a vessel at the process connection. The float arm assembly consists of a float at one end and a magnet at the other. As the liquid level in the vessel rises, the float rises, and the magnet falls. The magnet actuates a second magnet on the other side of the pressure boundary. This second magnet causes the switch to change state.
The pressure boundary contains no seals; it is a solid stainless steel barrier that passes a magnetic field, but no liquids. It is impossible for the process liquid to enter the switch enclosure through this barrier. The electrical contacts consist of a microswitch that can be either a Single-pole, Double-throw (SPDT) or Double-pole, Double-throw
(DPDT) Configuration. The SPDT Switch is available with either a 5 Amp or 8 Amp current load. The DPDT switch option is available with a 4 Amp Vac or 5 Amp Vdc
current load.
SPECIFICATIONS
• Maximum operating pressure of 2000 psig.
• Minimum operating specific gravity of 0.53.
• Operating temperature range of -67° F to 257° F; High temperature option -15˚F to 400˚F
• Available with 5A SPDT, 8A SPDT and 4A DPDT (*See switch specifications for full switch ratings).
• Printed circuit board mounted switches and terminal block means wiring electrical connections is easy. No wire splicing is required.
• All wetted parts including switch body are manufactured from 303 Stainless Steel. 316 Stainless Steel wetted parts option available.
• Magnetic Switch actuator operates through a solid steel barrier. There are no seals between the process and the switch compartment that could potentially cause a switch failure.
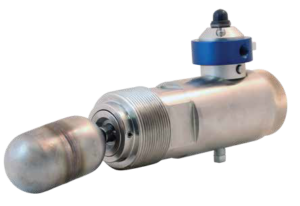
Features: The Model KPFS uses a float to determine the presence or absence of liquid in a vessel at the process connection. The float arm assembly consists of a float at one end and a magnet at the other. As the liquid level in the vessel rises, the float rises, and the magnet falls. The magnet actuates a second magnet on the other side of the pressure boundary. This second magnet is the reactive component in the snap-acting switch that opens and closes the pneumatic valve. Because of the nature of the design, adjustment is rarely, if ever needed. In the event that adjustment is needed, an easy-to-use adjustment screw is provided. The model KPFS is used to actuate pneumatic dump valves, such as the Kenco Model KDV series dump valve, to control liquids in separators, scrubbers, etc.
The pressure boundary contains no seals; it is a solid stainless steel barrier that passes a magnetic field, but no liquids. It is impossible for the process liquid to enter the switch enclosure through this barrier. The Model KPFS Pneumatic Float Switch can be ordered to have the pneumatic valve open when it senses a liquid level rising (-LR option) or open when it senses the liquid level falling (-LF option). A manual valve actuator is provided to open the valve manually if desired.
SPECIFICATIONS
• Maximum operating pressure of 2000 psi
• Minimum operating specific gravity of 0.53
• Pneumatic valve pressure range of 30 psi to 75 psi
• All wetted parts including the switch body are manufactured from 303/304 Stainless Steel. 316 Stainless Steel wetted parts option available.
• Magnetic Switch actuator operates through a solid stainless steel barrier. There are no seals between the process and the switch compartment that could potentially cause a switch failure.
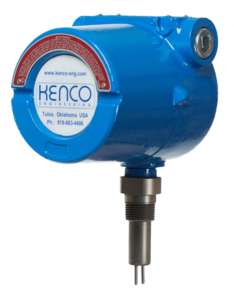
Features: Kenco’s Thermal Differential Switches are designed for a wide range of flow and level applications. These switches can be used to detect either the overall liquid level or a liquid – liquid interface. They can also be used to detect a specific flow rate or a flow/no flow condition in liquids and gasses.
Level and Interface Detection
Flow Detection for Liquids and Gasses
Fast Response Time
No Moving Parts
Temperature Compensation