Ball Valves - Medium + Low Pressure
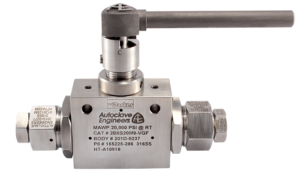
Features: Parker Autoclave Engineers high-pressure ball valves have been designed to provide superior quality for maximum performance within a variety of valve styles, sizes, and process connections. High pressure manual 2 way ball valves. 1/4″, 3/8″, 1/2″ and 1″ with working pressures to 20,000 psi ( 1379 bar). Features our one piece trunion mounted stem.
One-piece, trunnion mounted style, stem design eliminates shear failure and reduces the effects of side loading found in two piece designs.
• Re-torqueable seat glands for longer seat life.
• PEEK seats offer excellent resistance to chemicals, heat, and wear/abrasion.
• Full-port flow path minimizes pressure drop.
• 316 cold worked stainless steel construction.
• Low friction pressure assisted graphite filled PTFE stem seal increases cycle life and reduces operating torque.
• Quarter turn from open to close with positive stop.
• Viton o-rings for operation from 0°F (-17.8°C) to 400°F (204°C).
• Optional o-rings available for high-temperature applications.
• Optional wetted materials.
• Wide selection of tube and pipe end fittings available.
• Electric and pneumatic actuator options.
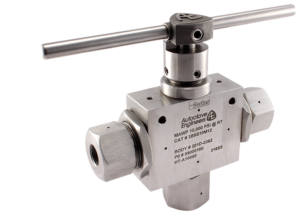
Features: Parker Autoclave Engineers high-pressure ball valves have been designed to provide superior quality for maximum performance within a variety of valve styles, sizes, and process connections. High pressure manual 3 way ball valves. 1/4″, 3/8″, 1/2″ with working pressures to 20,000 psi (1379 bar). Features our one piece trunion mounted stem.
• One-piece, trunnion mounted style, stem design eliminates shear failure found in two piece designs and reduces effects of side loading.
• Re-torqueable seat glands for longer seat life.
• Carbon filled PEEK seats offer excellent resistance to chemicals, heat, and wear/abrasion.
• Full-port flow path minimizes pressure drop.
• 316 cold worked stainless steel construction.
• Low friction pressure assisted graphite filled PTFE stem seal increases cycle life and reduces operating torque.
• Available in 90° turn diverter and 180° turn switching models.
• Viton o-rings for operation from 0°F (-17.8°C) to 400°F (204°C).
• Optional o-rings available for high-temperature applications.
• Optional wetted materials.
• Wide selection of tube and pipe end fittings available.
• Electric and pneumatic actuator options.
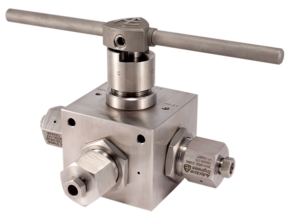
Features: Parker Autoclave Engineers high-pressure ball valves have been designed to provide superior quality for maximum performance within a variety of valve styles, sizes, and process connections. High pressure manual 4 way ball valves. 3/8″ with working pressures to 10,000 psi ( 690 bar). Features our one-piece trunion mounted stem.
• One-piece, trunnion mounted style, stem design eliminates shear failure found in two piece designs and
reduces the effects of side loading.
• Re-torqueable seat glands for longer seat life.
• Carbon filled PEEK seats offer excellent resistance to chemicals, heat, and wear/abrasion.
• Full-port flow path minimizes pressure drop.
• 316 cold worked stainless steel construction.
• Low friction pressure assisted graphite filled PTFE stem seal increases cycle life and reduces operating torque.
• Quarter turn crossover, and the half turn four way switching models available.
• Viton o-rings for operation from 0°F (-17.8°C) to 400°F (204°C).
• Optional o-rings available for high-temperature applications.
• Optional wetted materials.
• Wide selection of tube and pipe end fittings available.
• Electric and pneumatic actuator options.
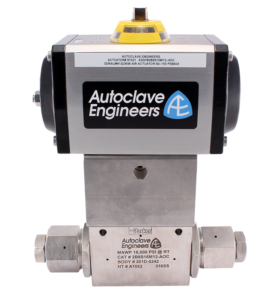
Features: Parker Autoclave Engineers ball valves can be supplied with either pneumatic or electric operators for automated or remote operation. Pneumatic and electric operators can be supplied with a variety of features and options. Operators are sized for each valve series to provide reliable and trouble free operation. Listed below are the operator features and available options.
Pneumatic Operators
• Used for remote and automatic operation
• Air-to-open/spring-to-close
• Air-to-close/spring-to-open
• Air-to-open and close (double acting)
• Limit switches or limit switches with visual indicators available
• High temperature option available.
• Stainless steel housing for corrosive applications available.
• Optional solenoid valve available
• Standard anodized aluminum housing
• Optional epoxy coated housing available Electric Operators
• Interface with control systems for automated operation and monitoring
• 120 & 220 VAC, 50/60 Hz standard
• 24VDC
• Explosion proof available
• CE mark available

Features: Parker Autoclave Engineers series 6DB double block valve is a two-stem ball valve providing an economical and convenient method of blocking and bleeding in applications such as pressure monitoring and test, chemical injection and drain line isolation. This full port quarter turn double ball valve is designed for operation up to 15,000 psi (1034 bar).
• One piece, trunnion mounted stem design eliminates shear failure and reduces the effects of side loading found in two piece designs.
• Re-torqueable seat glands for longer seat life.
• Carbon filled PEEK seats offer excellent resistance to chemicals, heat and wear/abrasion.
• Vee-stem vent valve.
• Full-port flow path minimizes pressure drop.
• 316 cold worked stainless steel construction.
• Low friction pressure assisted graphite filled PTFE stem seal increases cycle life and reduces operating torque.
• Quarter turn from open to close with positive stop.
• Viton o-rings for operation from 0°F (-17.8°C) to 400°F (204°C).
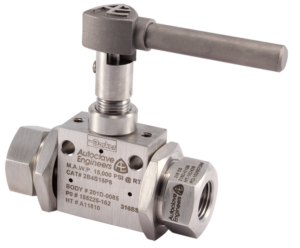
Features: Parker Autoclave Engineers subsea ball valves have been designed to fulfill the ever growing demand in the petroleum industry as well as the need for externally pressurized components in other markets. Utilizing the same design technology as the standard ball valve, the subsea design incorporates the necessary design alterations to provide a reliable externally pressurized valve for the subsea industry. With the availability of fittings, tubing, and related equipment our ball valves can provide all your needs on high-pressure applications above or below the surface.
• One-piece, trunnion mounted style, stem design eliminates shear failure found in two-piece designs.
• Re-torqueable seat glands for longer seat life.
• PEEK seats which offer excellent resistance to chemicals, heat, and wear/abrasion.
• Full-port flow path minimizes pressure drop.
• 316 cold worked stainless steel construction.
• Buna-N o-ring standard 250°F (121°C) max.
• Low friction pressure assisted graphite filled PTFE stem seal increases cycle life.
• Wide selection of tube and pipe end fittings available.
• Available to NACE MR-01-75.
• Optional wetted materials.
• Available in a number of flow configurations and port sizes.
Check + Relief Valves
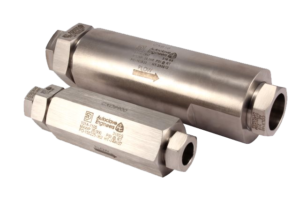
Features: Parker Autoclave Engineers Inline Check Valves provide unidirectional flow and tight shut-off for liquids and gas with high reliability. When differential drops below cracking pressure*, valve shuts off. The Ball Check Valve has all-metal components, allowing it to be used up to 1200°F (649°C).
Materials: 316 Stainless Steel: body, cover, poppet, cover gland. 300 Series Stainless Steel: spring. Standard O-ring: Viton, for operation to 400° F (204°C). Buna-N or PTFE available for 250°F (121°C) or 400°F (204°C) respectively; specify when ordering. *Cracking Pressure: 20 psi (1.38 bar) ±30%. Springs for higher cracking pressures (up to 100 psi (6.89 bar) available on special order for O-ring style check valves only.
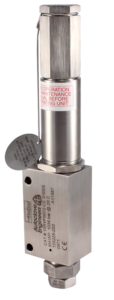
Features: Parker Autoclave Engineers relief valves provide reliable venting of gases or liquids for set pressures from 1,500 psi (103 bar) to 75,000 psi (5171 bar). These precision valves are designed for pressure gas systems, cryogenic systems, petrochemical applications and other special systems.
Series RVS relief valves utilize a soft seat design for reliable venting of gases at set pressures from 1,500 psi (103 bar) to 20,000 psi (1378 bar). The operating temperature range is 32°F (0°C) to 400°F (204°C). Series RVP relief valves provide reliable venting of gases or liquids for set pressures from 3,000 psi (206.8 bar) minimum to 75,000 psi (5171 bar). The standard temperature range for all models is -423° to 400° (-252° to 204°C). A high temperature option to 750°F (399°C) is also available.
Extreme Temperature Valves
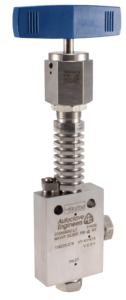
Features: Parker Autoclave Engineers has two different styles of valves for extreme temperature. Standard valves can be supplied with packing for operation from -100°F (-73°C) to 800°F (427°C), or with the addition of an extended packing housing for operation from -423°F (-252°C) to 1200°F (649°C). The extended packing housing provides the means of removing the packing from the extreme temperature medium. Machined grooves on the housing act as a heatsink to remove heat or cold. The second, which is economically priced, is a modified standard designed for the power industry. It operates to 1200°F (649°C) with graphite packing and no extended packing housing.
Extreme Temperature Valve Features:
• The extreme temperature option can be ordered on low, medium, high, micro-metering and other valve series.
• Reliable long life operation with extended stuffing box at very high and low temperatures.
• Design available for operation to 1200°F (649°C) without extended packing housing.
• Available with a variety of tubing connections and orifice sizes.
• Non-rotating stem.
• Wide range of material options
• Adjustable packing below threads.
• Metal to metal seating.
• Anti-extrusion back-up rings.
Fittings + Tubing - High Pressure (up to 150,000 psi)
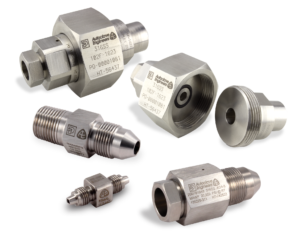
Features: Parker Autoclave Engineers offers a complete line of standard adapters and couplings as well as special designs and materials.
Parker Autoclave Engineer’s standard adapters are available in low, medium, and high pressure configurations. Standard adapters are machined from cold worked stainless steel. Other materials are available upon request.
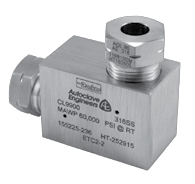
Features: Parker Autoclave Engineers high pressure fittings Series F and SF are the industry standard for pressures to 150,000 psi (10342 bar). Utilizing Parker Autoclave Engineers high pressure coned-and-threaded connections, these fittings are correlated with Series 30SC, 43SC, 30VM, 40VM, 60VM, 100VM, and 150V valves and Parker Autoclave Engineers high pressure tubing.
High Pressure Fittings, Tubing and Nipples Features:
• Coned-and-Threaded Connection.
• Available sizes are 1/4, 5/16, 3/8, 9/16, and 1”.
• Fittings manufactured from 316 cold worked or high strength stainless steel.
• Tubing is manufactured from dual rated 316/316L and 304/304L cold worked stainless steel.
• Operating Temperatures from -423°F (-252°C) to 1200°F (649°C).
• Anti-vibration connection components available.
• Ultra-high pressure components.
• Autofrettaged tubing.
• High pressure high cycle tubing.
Fittings + Tubing - Low Pressure (up to 15,000 psi)
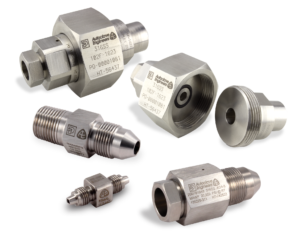
Features: Parker Autoclave Engineers offers a complete line of standard adapters and couplings as well as special designs and materials.
Parker Autoclave Engineer’s standard adapters are available in low, medium, and high pressure configurations. Standard adapters are machined from cold worked stainless steel. Other materials are available upon request.
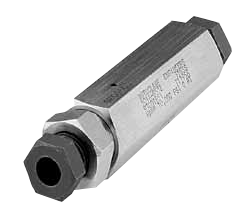
Features: Parker Autoclave Engineers Low Pressure Fittings are designed for use with low pressure valves and tubing. These fittings feature improved SpeedBite compression connections with larger orifices for excellent flow capabilities. Parker Autoclave Engineers fittings and components are manufactured of cold-worked type 316 stainless steel. Optional materials are available upon request.
Low Pressure Fittings and Tubing Features:
• Single-ferrule compression sleeve.
• Fast easy make-up of connection.
• Available sizes are 1/16”, 1/8”, 1/4”, 3/8”, & 1/2”.
• Fittings manufactured from cold worked 316 stainless steel.
• Tubing is manufactured from dual rated 316/316L and 304/304L annealed stainless steel.
• All items available in special materials.
• Operating temperatures from -100°F (-73°C) to 650°F (343°C).
• Molybdenum disulfide-coated gland nuts to prevent galling.
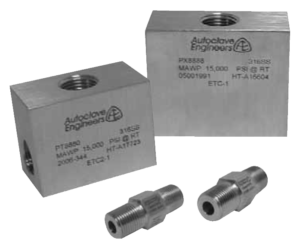
Features: Parker Autoclave Engineers pipe fittings, P Series, are designed for liquid and gas applications. Available from 1/4″ to 1″ NPT to 15,000 psi and temperatures to 400°F (204°C).
Pipe Fittings, Tubing and Nipples Features:
• Available sizes are 1/4″, 3/8″, 1/2″, 3/4″ and 1″
• Fittings and tubing manufactured from cold worked 316 stainless steel.
• Operating Temperatures from -423°F (-252°C) to 400°F (204°C).
Fittings + Tubing - Medium Pressure (up to 20,000 psi)
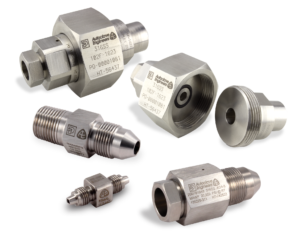
Features: Parker Autoclave Engineers offers a complete line of standard adapters and couplings as well as special designs and materials.
Parker Autoclave Engineer’s standard adapters are available in low, medium, and high pressure configurations. Standard adapters are machined from cold worked stainless steel. Other materials are available upon request.
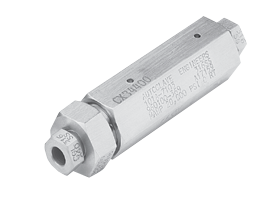
Features: Parker Autoclave Engineers medium pressure fittings, Series SF, are designed for use with Series 20SM medium pressure valves and Parker Autoclave Engineers’ medium pressure tubing. They incorporate medium pressure coned-and-threaded connections with orifices sized to match the high-flow Series 20SC valves.
Medium Pressure Fittings, Tubing and Nipples Features:
• Coned-and-Threaded Connection.
• Available sizes are 1/4″, 3/8″, 9/16″, 3/4″, 1″ and 1-1/2″.
• Fittings manufactured from cold worked 316 stainless steel.
• Tubing is manufactured from dual rated 316/316L and 304/304L cold worked stainless steel.
• Operating Temperatures from -423°F (-252°C) to 1200°F (649°C).
• Anti-vibration connection components available.
• All items available in special material.
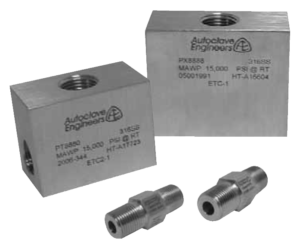
Features: Parker Autoclave Engineers pipe fittings, P Series, are designed for liquid and gas applications. Available from 1/4″ to 1″ NPT to 15,000 psi and temperatures to 400°F (204°C).
Pipe Fittings, Tubing and Nipples Features:
• Available sizes are 1/4″, 3/8″, 1/2″, 3/4″ and 1″
• Fittings and tubing manufactured from cold worked 316 stainless steel.
• Operating Temperatures from -423°F (-252°C) to 400°F (204°C).
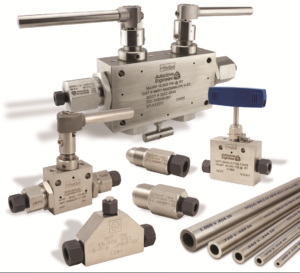
Features: Parker Hannifin MPI™ connections are engineered and manufactured to be secure and gas-tight while being made manually (wrench turns) or hydraulically using a set tool. This connection has application throughout industry, including offshore oil and gas exploration platforms, research labs, and other facilities that require operating pressures to 15,000 psi. MPI™ Fittings are ideally suited to handle liquids, gases, or chemicals and can be used on a wide variety of tubing materials including Instrument Grade thick-walled annealed 316 SS, 1/8th Hard (cold drawn) 316 SS MPI tubing, and 2507 Super Duplex MPI tubing. Every Parker MPI™ Fitting is supplied complete with both ferrules and compression gland nut, ready to install.
Features & Benefits:
• Front ferrule with corrosion-resistant Parker Suparcase® forms a seal between the tube, body and ferrule. It also provides a mechanical hold on the tube.
• Back ferrule with corrosion-resistant Parker Suparcase® provides a strong mechanical hold on the tube.
• Longer thread area for improved resistance to pressure and load on the ferrules.
• Molybdenum disulfide-coated inverted nut helps prevent galling, provides easier assembly and permits multiple remakes.
• Long tube-support area improves resistance to vibration and the line loads.
MPI™ Fittings Pressure Ratings
The maximum pressure rating is marked on each fitting. MPI™ working pressures to be determined by selected tubing.
• Size 4 (1/4″) MPI™ – to 15,000 psi
• Size 6 (3.8″) MPI™ – to 15,000 psi
• Size 8 (1/2″) MPI™ – to 15,000 psi
• Size 9 (9/16″) MPI™ – to 15,000 psi
• Size 12 (3/4″) MPI™ – to 15,000 psi
• Size 16 (1″) MPI™ – to 12,500 psi using 316 SS MPI tubing, 15,000 psi using MPI 2507 Super Duplex tubing with -XF Ferrule Option
Note: Tube and pipe thread sizes are designated by the number of sixteenths of an inch (1/4” tube = 4/16” or 4).
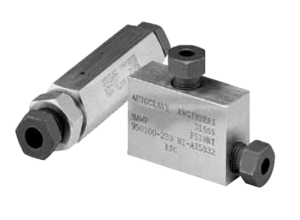
Features: Parker Autoclave Engineers Medium Pressure QS Fittings are designed for use with QS Series valves and medium pressure tubing. These fittings feature improved compression connections with larger orifices for excellent flow capabilities. Parker Autoclave Engineers fittings and components are manufactured of high strength stainless steel.
QS Medium Pressure Fittings and Tubing:
• Available sizes are 1/4, 3/8, 9/16, 3/4 and 1”.
• Fittings and tubing manufactured from high strength stainless steel.
• Molybdenum disulfide-coated gland nuts to prevent galling.
• Gland nut positioning mark for assembly.
• Single-ferrule compression sleeve.
• Connection weep holes for safety and leak detection.
• Fast easy make-up of connection.
• Operating Temperatures from 0°F (-17.8°C) to 650°F (343°C).
• 1″ QS fitting bodies are 2507 Super Duplex standard.
Hydraulic Control + Relief Valves
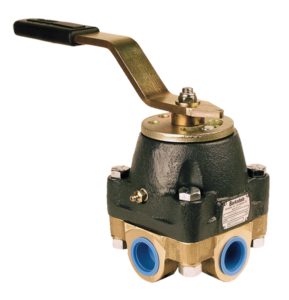
Features: Heavy Duty Valves
Heavy Duty Line – directional control for fluids and gasses up to 6,000 psi
Shear-Seal® Manual Control Valve
Applications
Land-based and offshore drilling equipment
Steel mills
Nitrogen charging panels
Refineries and chemical processing plants
Power generation facilities
Working Pressure: Air (pneumatic) up to 4,000 psi (276 bar)
hydraulic oil or lubricated water up to 6,000 psi (413 bar)
Flow Capacity, Cv: See table
Back Pressure: Must not exceed 250 psi (17.2 bar) at return port for satisfactory operation
Pressure Drop: 14 psi (0.96 bar) at 20 ft/sec
See Supplemental Guide for more detailed information
Proof Pressure: 1-1/2 times working pressure except at return port
Burst Pressure: 2-1/2 times working pressure except at return port (3,000 psi [206 bar])
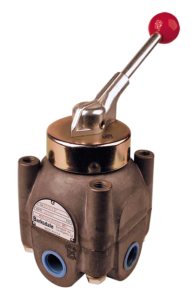
Features: High Pressure OEM Valves
High Pressure OEM Valve line up to 3000 psi
Shear-Seal® Manual Control Valve
Applications
Hydraulic presses
Military equipment
Paper mill controls
Hydraulic pilot valves
Railroad maintenance equipment
Halon fill systems
Working Pressure: Hydraulic fluid up to 3000 psi (206 bar)
Back Pressure: Must not exceed 250 psi (17.2 Bar) at return port for satisfactory operation
Pressure Drop: 14 psi (0.96 bar) at 20 ft/sec
See Supplemental Guide for more detailed information
Proof Pressure: 1-1/2 times working pressure except at return port
Burst Pressure: 2-1/2 times working pressure except at return port (3000 psi [206 bar])
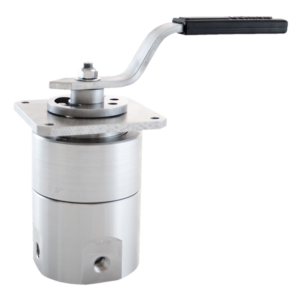
Features: High Pressure Valve
Shear-Seal® high pressure directional control valve for fluids and gasses up to 15,000 psi
Applications
Offshore drilling equipment
Refineries and chemical processing plants
Gas compression systems
Marine umbilical reels
Working Pressure: Standard to 10,000 psi (690 bar)
Optional to 15,000 psi (1,034 bar) (on 1/4” model only)
Flow Capacity, Cv: See table
Back Pressure: Must not exceed 250 psi (17.2 bar) at return port for satisfactory operation
Pressure Drop: 14 psi (0.96 bar) at 20 ft/s
Proof Pressure: 1-1/2 times working pressure except at return port
Burst Pressure: 2-1/2 times working pressure except at return port (3,000 psi [206 bar]) maximum
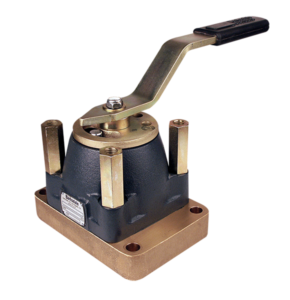
Features: Subplate Mounted Heavy Duty Valve
Sub-plate mounted manifold valve – Shear-Seal® directional control for fluids and gasses up to 4,500 psi
Applications
Steel mills
Shipboard hydraulic control systems
Refineries and chemical processing plants
Power generation facilities
Working Pressure: Hydraulic oil or lubricated water up to 4,500 psi (310 bar)
Flow Capacity, Cv: See table
Back Pressure: Must not exceed 250 psi (17.2 Bar) at return port for satisfactory
operation
Pressure Drop: 14 psi (0.96 bar) at 20 ft/sec
* See Supplemental Guide for more detailed information
Proof Pressure: 1-1/2 times working pressure except at return port
Burst Pressure: 2-1/2 times working pressure except at return port (3,000 psi [206 bar])
Media Temperature
Range:
-40° to +250°F (-40° to +121°C)
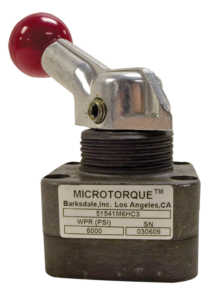
Features: Barksdale’s Microtorque® valve provides superior directional control for fluid power applications up to 6,000 psi where compact design and virtually zero leakage* are a must. Utilizing Barksdale’s Shear-Seal® technology, the Microtorque® valve offers reliable performance and lapped metal-to-metal sealing surfaces that will easily tolerate contaminated fluids. This valve offers many options that make it extremely versatile including panel mounting, spring return, 2 or 3 position detents, DO3 manifold mounting, and non-interflow. Leveraging the flexibility and unique features of the Microtorque® valve, along with its superior performance, can result in bottom line savings and operational benefits for your customers.
Media: Hydraulic oil
Working Pressure: 6,000 psi (415 bar) **
Flow Capacity, Cv: See table
Back Pressure: Must not exceed 250 psi (17.2 bar)*** at return port for satisfactory operation
Proof Pressure: 1-1/2 times working pressure except at return port
Burst Pressure: 2-1/2 times working pressure except at return port
Media Temperature
Range:
-40° to +250°F (-40° to +121°C)
Porting: 1/4” NPT, SAE for 1/4” tubing, or DO3 pattern for manifold mounting
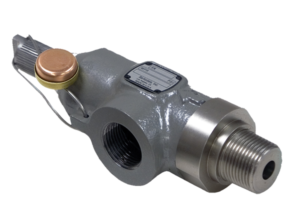
Features: The Model 8014, part of the new 8010 series, incorporates all the manufacturing knowledge and experience that has earned Barksdale a reputation for top quality and reliability in the market. This unit is a 3/4″ NPT relief valve intended for use in hydraulic systems. All stainless steel internals and a corrosion-resistant powder-coated external housing makes this product perfect for heavy industrial environments in the most demanding applications.
Working Pressure: Hydraulic oil up to 5500 psi (380 bar)
Proof Pressure: 10,000 psi (690 bar)
Pressure Ranges: 200 – 500 psi (15 – 35 bar)
500 – 1500 psi (35 – 105 bar)
1500 – 3500 psi (105 – 240 bar)
3500 – 5500 psi (240 – 380 bar)
Flow Rate: 15 GPM (NOMINAL)
Wetted Material: Fitting: Heat-treated 410 stainless steel
Internals: 416 stainless steel
Spring: Powder-coated high strength steel
Ball: Tungsten Carbide
Housing: Powder-coated ductile iron
Pressure Connection: 3/4” NPTM x 3/4” NPTF
Temperature Range: -40° to +200°F (-40° to +93°C)
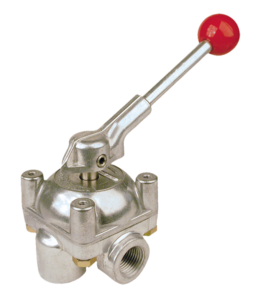
Features: Barksdale’s Series 9000 Valves control hydraulic fluids and gasses up to 350 psi. Featuring Barksdale’s famous Shear-Seal® technology, the Series 9000 Valves offer dependable performance and long life for manual control of commercial and industrial process applications. The versatile design of this valve offers the ability to tailor the perfect configuration to meet your installation requirements.
Working Pressure: Pneumatic or hydraulic from 150
psi to 350 psi (10.3 to 24.1 bar); see table
Cv, Minimum Orifice: See table
Back Pressure: Must not exceed 250 psi (17.2 bar) at return port for satisfactory operation
Proof Pressure: 1-1/2 times working pressure except at return port (without damage to valve)
Burst Pressure: 2-1/2 times working pressure except at return port (300 psi, 20.7 bar)
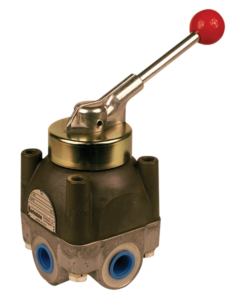
Features: Barksdale’s Low Pressure OEM Valve line provides exceptional directional control for fluids and gasses up to 500 psi in the toughest industrial applications. Using Barksdale’s Shear-Seal® technology the OEM Valve products offer dependable performance and long life even when the media being controlled is contaminated with debris that would ruin ordinary valves. Flexibility is built into the Low Pressure OEM Valve line which features several standard options that can be adapted to meet the unique needs that OEM customers require in their products.
Working Pressure: Gasses or hydraulic fl uids up to 500 psi (34 bar)
Flow Capacity, Cv: See table
Back Pressure: Must not exceed 250 psi (17.2 bar) at return port for satisfactory operation
Pressure Drop: 14 psi (0.96 bar) at 20 ft/sec
See Supplemental Guide for more detailed information
Proof Pressure: 1-1/2 times working pressure except at return port
Burst Pressure: 2-1/2 times working pressure except at return port (500 psi [34 bar])
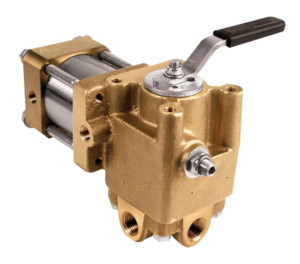
Features: Barksdale’s patented Series II valve provides an optimal solution by combining the dependable features of our heavy duty Shear-Seal® valves with the reliability of a rack and pinion pilot actuator, all in one integrated package. With the ability to handle high velocity flows at pressures up to 6000 psi and tolerate contaminated media, the Series II valve becomes the choice for the toughest applications.
Working Pressure: Hydraulic up to 3,000 or 6,000 psi (206 bar or 413 bar)
Air up to 2,000 or 4,000 psi (138 or 276 bar)
Back Pressure: Must not exceed 250 psi (17.2) bar at return port for satisfactory operation
Proof Pressure: 1-1/2 times working pressure except at return port
Burst Pressure: 2-1/2 times working pressure except at return port (3,000 psi [206 bar])
Pressure Drop
(all Valves):
Porting: 1/4”, 3/8”, 1/2”, 3/4”, 1”, & 1-1/2”
NPT Standard (SAE J1926 Option)
Media Temperature
Range:
-40° to +250°F (-40° to +121°C)
Needle Valves - High Pressure (up to 150,000 psi)
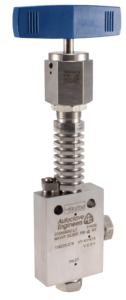
Features: Parker Autoclave Engineers has two different styles of valves for extreme temperature. Standard valves can be supplied with packing for operation from -100°F (-73°C) to 800°F (427°C), or with the addition of an extended packing housing for operation from -423°F (-252°C) to 1200°F (649°C). The extended packing housing provides the means of removing the packing from the extreme temperature medium. Machined grooves on the housing act as a heatsink to remove heat or cold. The second, which is economically priced, is a modified standard designed for the power industry. It operates to 1200°F (649°C) with graphite packing and no extended packing housing.
Extreme Temperature Valve Features:
• The extreme temperature option can be ordered on low, medium, high, micro-metering and other valve series.
• Reliable long life operation with extended stuffing box at very high and low temperatures.
• Design available for operation to 1200°F (649°C) without extended packing housing.
• Available with a variety of tubing connections and orifice sizes.
• Non-rotating stem.
• Wide range of material options
• Adjustable packing below threads.
• Metal to metal seating.
• Anti-extrusion back-up rings.
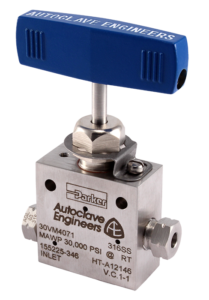
Features: Parker Autoclave Engineers high-pressure needle valves are available in seven different series for applications such as the chemical/petrochemical, water-blast, water-jet, research, and oil and gas industries. The Parker Autoclave Engineers high-pressure valve line utilizes a coned-and-threaded connection design providing a leak tight reliable connection for gas and liquid service. These valves are complemented by a complete line of fittings, tubing and accessories.
• Tubing sizes from 1/4” to 1”.
• Non-rotating stem prevents stem/seat galling.
• Rising stem/barstock body design.
• Metal-to-metal seating achieves bubble-tight shut-off, longer stem/seat life in abrasive flow, greater
durability for repeated on/off cycles and excellent corrosion resistance.
• For dependable stem and body sealing 30SC, 43SC and 30VM valves are furnished with PTFE
encapsulated packing; the 40VM and 60VM valves feature nylon/leather packing below threads.
• Stem sleeve and packing gland materials have been selected to achieve extended thread cycle life and
reduced handle torque.
• Choice of Vee or Regulating stem tips.
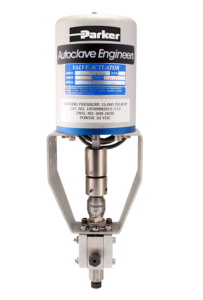
Features: Parker Autoclave Engineers has a flow control valve to remotely control process flow at high pressure for vital component to processing operations. Parker Autoclave Engineers’ control valve utilizes their standard Micro-metering valve coupled to an electric actuator. The combination of these two precision, high quality components, provide a superior low flow control valve for use with liquids and gases.
Electric Flow Control Valve Features:
• Sizes 1/8″, 1/4″ and 3/8″
• Cv: 0.004
• Precise, accurate control
• Temperatures: -100°F to +600°F
• End connections: low pressure and high pressure Autoclave
• Materials: 316 SS, special materials available
• Controller Enclosure Rating: IP65 Weatherproof
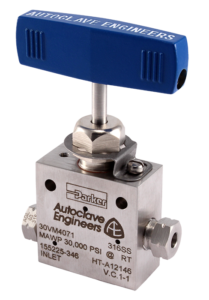
Features: Parker Autoclave Engineers offers a complete series of high pressure valves and fittings for wellhead christmas trees. Parker Autoclave Engineers components are designed and manufactured to meet or exceed API and other applicable specifications for wellhead equipment, as well as Parker Autoclave Engineers’ own exacting standards for safety, reliability and service life under high pressure operation. Parker Autoclave Engineers “SOG” components meet or exceed all requirements of NACE MR0175-2002.
Pressure/Temperature Ratings: Valves and fittings for standard service are rated for working pressure up to 60,000 psi (4137 bar) at 100°F (38°C). Type SOG components are rated up to 30,000 psi (2068 bar) at 100°F (38°C). Sizes: Parker Autoclave Engineers’ type SOG valves and fittings are supplied with standard API test and gauge connections (Parker Autoclave Engineers’ F562C).
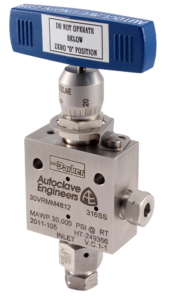
Features: Parker Autoclave Engineers MicroMetering valves are designed for applications where more precise control of small flows is required than is possible with a standard regulating stem. Barrel and Thimble micrometer design permits settings to be repeated. Metering is effected by a finely tapered stem acting in a precisely mated replaceable seat. Very fine stem position is achieved utilizing a 40 TPI thread. The Barrel and Thimble are set for proper metering at the factory.
MicroMetering Valve Features:
• Barrel and Thimble design permits repeatable settings.
• Barrel divisions every 0.025”
• 25 Thimble divisions, each representing 0.001” stem travel
• One revolution = 0.025” stem travel
• Cold-worked type 316 stainless steel body with stainless steel packing gland. Stem and seat are cold-worked type 316 stainless steel.
• Packing below stem threads is PTFE for the 10VRMM and 30VRMM valves and nylon leather for the 60VRMM. For packing options, see Technical Information Section.
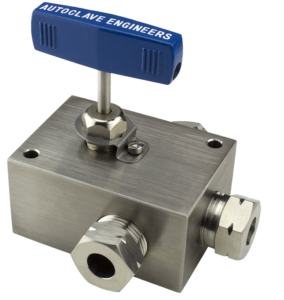
Features: Parker Autoclave Engineers’ Wellhead Gauge valves are designed for reliable shut-off service at a maximum working pressure of 30,000 psi (2068 bar). The Wellhead Gauge and Bleed Valves are standard in 316 stainless steel material. Special materials available on request.
Gauge Valve Features:
• One inlet, three outlet ports
• Metal-to-metal bubble tight shut-off
• Packing below stem threads
• Two piece non-rotating stem on standard valves
Bleed Valve Features:
• One piece hex construction allows easy installation
• Vent port tapped for plumbing to safe area
• Tee handle for easy operation
• Positive blow out prevention on stem
• 1/8” NPT outlet connection
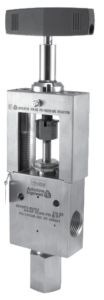
Features: Parker Autoclave Engineers’ yoke valves are extra heavy duty, plant grade instrument valves for industrial and severe service applications. Yoke valves feature low closing torque for ease of operation and are designed for use with Parker Autoclave Engineers medium and high pressure tubing and fittings.
Yoke Valve Features:
• Tubing sizes from 9/16” to 1”.
• Rising stem/barstock body design.
• Non-rotating stem prevents stem/seat galling.
• Metal-to-metal seating achieves bubble-tight shutoff, longer stem/seat life in abrasive flow, greater durability for repeated on/off cycles and excellent corrosion resistance.
Needle Valves Pressures to 50,000 psi (3447 bar)
Y Series Yoke
• PTFE encapsulated packing provides dependable stem and body sealing.
• Stem sleeve and packing gland materials have been selected to achieve extended thread
cycle life and reduced handle torque.
• Choice of Vee or Regulating stem tips.
• Available in two body patterns.
• Optional materials for cryogenic and other applications.
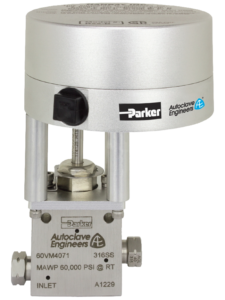
Features: The Parker Autoclave Engineers Explosion Proof Electric Flow Control valves are designed to operate up to 60,000 psi depending on the model number. The valves are “fail-as-is” meaning the valve maintains its last position on signal or power failure.
Electrical Power
Power Required: 24 VDC/72 Watt Maximum
Input Impedance: 250 Ohms (4-20 mA input)
Environmental
Atmosphere: NEC CLASS I, DIV 1, GROUP B,C,D
Operating Temperature (Actuator): -40º to 85º C
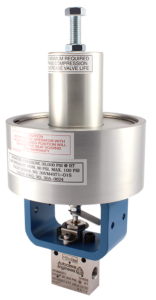
Features: Parker Autoclave Engineer’s valves are available with diaphragm or piston type actuators. Six sizes of air actuators (light, heavy light, medium, heavy duty or extra heavy, single and double stage) are offered to meet the service requirements of Parker Autoclave Engineer’s Low, Medium and High Pressure valves. Both air-to-open (normally closed) and air-to-close (normally open) designs are included in the product line. Optional air to open and close are available upon request.
Air Operator
• Maximum allowable working pressure: 100 psi (6.89 bar)
• Allowable diaphragm temperature range: -40°F to 200°F (-40°C to 93°C)
• Area of diaphragm: Light duty – 4.9 sq. in (31.6 sq. cm), Medium duty – 19.6 sq. in (126.5 sq. cm), Heavy duty – 45.66 sq. in (294.58 sq. cm)
• Approximate air usage/cycle @ 100 psi (6.89 bar): Light duty – .007 SCF (.00019 SCM), Medium duty – .07 SCF (.0019 SCM), Heavy duty – .2 SCF (.0056 SCM)
Needle Valves - Low Pressure (up to 15,000 psi)
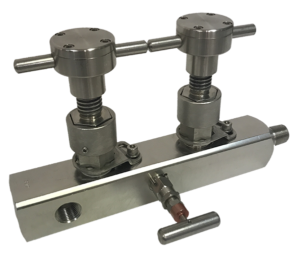
Features: Century gauge valves include multi-port and block and bleed styles suitable for gauge isolation, calibration and venting with a choice of either globe pattern or straight-thru bore designs. A wide choice of end connections and comprehensive range of standard gauge accessories allows complete flexibility for individual installations
Materials CS, SS, Monel®, Hastelloy®, Duplex and other exotic materials
Seat Metal and Soft
Connections 1/2” to 3/4” threaded, welded and flanged also available
Orifice Sizes 1/8” [3 mm], 3/16” [4.7 mm], 1/4” [6.4 mm], 3/8” [9.5 mm]
Pressure (max) 10,000 psig [690 barg]
Temperature (max) 1000°F [538°C]
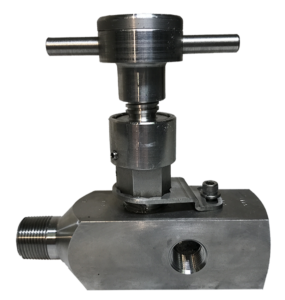
Features: Century large bore hand valves are suitable for all instrument isolation duties, giving you bubble tight shut-off time after time. With metal or soft seats for gas, vapor or liquid applications, rated up to 10,000 psig [690 barg] and available in a range of standard and exotic materials there is a hand valve for even the most severe service.
Materials CS, SS, Monel®, Hastelloy®, Duplex and other exotic materials
Seat Metal and Soft
Connections 1/4” to 1” threaded, welded and flanged also available
Orifice Sizes 1/8” [3 mm], 3/16” [4.7 mm], 1/4” [6.4 mm], 3/8” [9.5 mm], 5/8” [16 mm]
Pressure (max) 10,000 psig [690 barg]
Temperature (max) 1000°F [538°C]
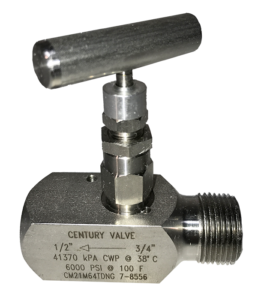
Features: Century hand valves are suitable for all instrument isolation duties, giving you bubble tight shut-off time after time. With metal or soft seats for gas, vapor or liquid applications, rated up to 10,000 psig [690 barg] and available in a range of standard and exotic materials there is a hand valve for even the most severe service.
Materials CS, SS, Monel®, Hastelloy®, Duplex and other exotic materials
Seat Metal and Soft
Connections 1/4” to 1” threaded, welded and flanged also available
Orifice Sizes 1/8” [3 mm], 3/16” [4.7 mm], 1/4” [6.4 mm], 3/8” [9.5 mm],
5/8” [16 mm]
Pressure (max) 10,000 psig [690 barg]
Temperature (max) 1000°F [538°C]
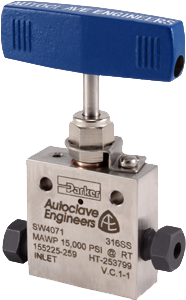
Features: These valves are a non-rotating rising stem design, working pressures to 15,000 psi (1034 bar). Tubing sizes range from 1/8″ to 1/2″. Tubing connections utilizes Parker Autoclave Engineers Speed Bite single ferrule design. Operating temperatures from 0°F to 650°F (-17.8°C to 343°C). 316 stainless steel construction, other options available.
Low Pressure Valve Features:
• 10V Series valve design provides in-line tube connections for 1/4” to 1/2” tube sizes.
• SW Series valve design provides increased flow capabilities.
• Tubing sizes from 1/8” to 1/2”.
• Rising stem/bar stock body design.
• Non-rotating stem prevents stem/seat galling.
• Metal-to-metal seating achieves bubble-tight shutoff, longer stem/seat life in abrasive flow, greater durability for repeated on/off cycles and excellent corrosion resistance.
• PTFE encapsulated packing provides dependable stem and body sealing.
• Stem sleeve and packing gland materials have been selected to achieve extended thread cycle life and reduced handle torque.
• Choice of Vee or Regulating stem tips.
• Available in five body patterns.
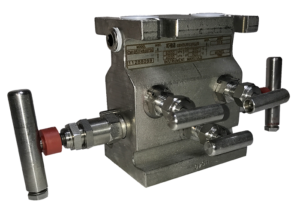
Features: Century Valve has the largest and most innovative range of ‘differential pressure’ flow and level manifolds available in the world with models available for every kind of D/P instrument. These include conventional three and five valve manifolds as well as purpose-designed models for special applications.
Materials CS, SS, Monel®, Hastelloy®, Duplex and other exotic materials
Seat Metal and Soft
Instrument Connections 1/4” to 1/2” threaded or flange mounting
Process Connections 1/4” to 1/2” threaded or flange mounting
Orifice Sizes 1/8” [3 mm], 3/16” [4.7 mm], 1/4” [6.4 mm], 3/8” [9.5 mm]
Pressure (max) 6000 psig [414 barg]
Temperature (max) 1000°F [538°C]
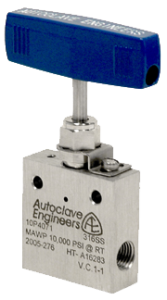
Features: All series are a non-rotating rising stem design, working pressures up to 15,000 psi (10,345 bar). Featuring FNPT pipe connections from 1/4″ to 1″. Operating temperatures from 0°F to 400°F (-17°C to 204°C). 316 stainless steel construction, other options available.
Pipe Valve Features:
• P Series valve design provides in-line pipe connections for 1/4” to 1” pipe sizes. 1/8 connections offset.
• Rising stem/bar stock body design.
• Non-rotating stem prevents stem/seat galling (1/8″ NPT rotating stem design).
• Metal-to-metal seating achieves bubble-tight shut-off, longer stem/seat life in abrasive flow, greater durability for repeated on/off cycles and excellent corrosion resistance.
• PTFE encapsulated packing provides dependable stem and body sealing.
• Stem sleeve and packing gland materials have been selected to achieve extended thread cycle life and reduced handle torque.
• Choice of Vee or Regulating stem tips.
• Operating temperature range from -423°F (-252°C) to 400°F (204°C).
Needle Valves - Medium Pressure (up to 20,000 psi)
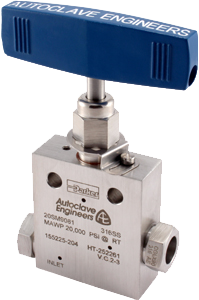
Features: Parker Autoclave Engineers Medium Pressure valves are a non-rotating rising stem design, working pressures to 20,000 psi (1379 bar). Tubing sizes range from 1/4″ to 1-1/2″.Tubing connections utilizes Parker Autoclave Engineers coned and threaded design. Operating temperatures from -423°F to 1200°F (-252°C to 649°C). 316 stainless steel construction, other options available.
Medium Pressure Valve Features:
• Largest-port valves available for medium pressure applications.
• Tubing sizes available from 1/4” to 1”.
• Rising stem/bar stock body design.
• Non-rotating stem prevents stem/seat galling.
• New one piece stem design permits ease of assembly and packing replacement.
• Metal-to-metal seating achieves bubble-tight shut-off, longer stem/seat life in abrasive flow, greater durability for repeated on/off cycles and excellent corrosion resistance.
• PTFE encapsulated packing provides dependable stem and body sealing.
• Stem sleeve and packing gland materials have been selected to achieve extended thread cycle life and reduced handle torque.
• Choice of Vee or Regulating stem tip.
• Available in five body patterns.
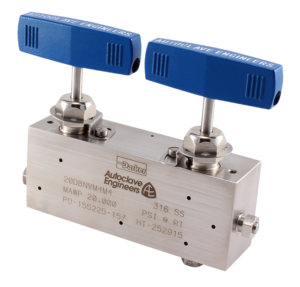
Features: Parker Autoclave Engineers series MVBB block and bleed valve is a two stem manifold valve providing an economical and convenient method of blocking, bleeding and calibrating pressure transmitters and gauges. The valve utilizes the mini valve packing and stem design making it compact and easy to use. The valve can be surface or panel mounted for safe operation. In addition, manifold style valves reduce the number of fittings and space required for installation.
Block and Bleed Features:
• MVBB Series valve design provides large valve performance in a small package
• Tubing sizes: 1/4″ and 3/8″
• Rising stem/bar stock body design.
• Metal-to-metal seating achieves bubble-tight shut-off, longer stem/seat life in abrasive flow, greater durability for repeated on/off cycles and excellent corrosion resistance.
• PTFE encapsulated packing provides dependable stem and body sealing.
• Stem and packing gland design have been selected to achieve extended thread cycle life and reduced handle torque.
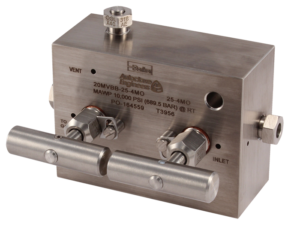
Features: Designed for blocking, bleeding, and calibration. This valves is a rotating rising stem design, rated to 20,000 psi (1379 bar). Tubing size 1/4-1″. Tubing connections utilizes the coned joint design. Operating temperatures from 0°F to 450°F (-17.8°C to 232°C). 316 stainless steel construction, other options available.
Block and Bleed Features:
• 20DBNV Series valve design provides large valve performance in a small package.
• Tubing sizes: 1/4″ to 1″.
• Rising stem/barstock body design.
• Metal-to-metal seating achieves bubble-tight shut-off, longer stem/seat life in abrasive flow, greater durability for repeated on/off cycles and excellent corrosion resistance.
• PTFE encapsulated packing provides dependable stem and body sealing.
• Stem and packing gland design have been selected to achieve extended thread cycle life and reduced handle torque.
• Temperatures from -100°F (-73°C) to 600°F (316°C)
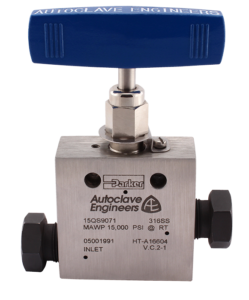
Features: Parker Autoclave Engineers Medium Pressure 15K valves are a non-rotating rising stem design, working pressures to15,000 psi (1034 bar). Tubing size: 1-1/2″. Tubing connections utilizes Parker Autoclave Engineers coned and threaded design. Operating temperatures from -423°F to 1200°F (-252°C to 649°C). 316 stainless steel construction, other options available.
Medium Pressure Valve Features:
• Largest-port valve available for medium pressure applications.
• Tubing size 1-1/2″.
• Rising stem/barstock body design.
• Non-rotating stem prevents stem/seat galling.
• New one piece stem design permits ease of assembly and packing replacement.
• Metal-to-metal seating achieves bubble-tight shut-off, longer stem/seat life in abrasive flow, greater durability for repeated on/off cycles and excellent corrosion resistance.
• PTFE encapsulated packing provides dependable stem and body sealing.
• Stem sleeve and packing gland materials have been selected to achieve extended thread cycle life and reduced handle torque.
• Choice of Vee or Regulating stem tip.
• Available in two body patterns.
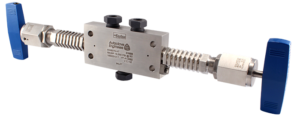
Features: Parker Autoclave Engineers diverter valves provide the ability to direct incoming flow to one of two outlets. Flow is changed by rotating the handle in or out causing a double-ended stem to block the flow path to the outlet not needed. Diverter valves eliminate the need for multiple valves and the possibility of error in flow direction changes.
AE Diverter Valve Features:
• Diverts incoming flow to one of two outlet lines.
• Tubing sizes from 9/16” to 1”.
• Rising stem/bar stock body design.
• Non-rotating stem prevents stem/seat galling.
Needle Valves Pressures to 20,000 psi (1379 bar) 20DV Series Diverter
• Metal-to-metal seating achieves bubble-tight shut-off, longer stem/seat life in abrasive flow, greater durability for repeated on/off cycles and excellent corrosion resistance.
• PTFE encapsulated packing provides dependable stem and body sealing.
• Stem sleeve and packing gland materials have been selected to achieve extended thread cycle life and reduced handle torque.
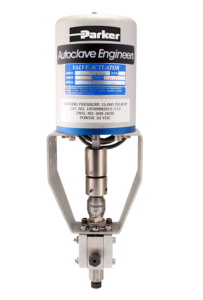
Features: Parker Autoclave Engineers has a flow control valve to remotely control process flow at high pressure for vital component to processing operations. Parker Autoclave Engineers’ control valve utilizes their standard Micro-metering valve coupled to an electric actuator. The combination of these two precision, high quality components, provide a superior low flow control valve for use with liquids and gases.
Electric Flow Control Valve Features:
• Sizes 1/8″, 1/4″ and 3/8″
• Cv: 0.004
• Precise, accurate control
• Temperatures: -100°F to +600°F
• End connections: low pressure and high pressure Autoclave
• Materials: 316 SS, special materials available
• Controller Enclosure Rating: IP65 Weatherproof
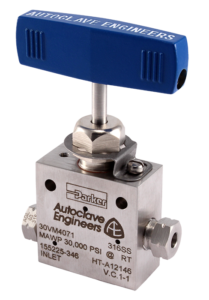
Features: Parker Autoclave Engineers offers a complete series of high pressure valves and fittings for wellhead christmas trees. Parker Autoclave Engineers components are designed and manufactured to meet or exceed API and other applicable specifications for wellhead equipment, as well as Parker Autoclave Engineers’ own exacting standards for safety, reliability and service life under high pressure operation. Parker Autoclave Engineers “SOG” components meet or exceed all requirements of NACE MR0175-2002.
Pressure/Temperature Ratings: Valves and fittings for standard service are rated for working pressure up to 60,000 psi (4137 bar) at 100°F (38°C). Type SOG components are rated up to 30,000 psi (2068 bar) at 100°F (38°C). Sizes: Parker Autoclave Engineers’ type SOG valves and fittings are supplied with standard API test and gauge connections (Parker Autoclave Engineers’ F562C).
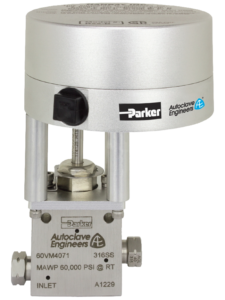
Features: The Parker Autoclave Engineers Explosion Proof Electric Flow Control valves are designed to operate up to 60,000 psi depending on the model number. The valves are “fail-as-is” meaning the valve maintains its last position on signal or power failure.
Electrical Power
Power Required: 24 VDC/72 Watt Maximum
Input Impedance: 250 Ohms (4-20 mA input)
Environmental
Atmosphere: NEC CLASS I, DIV 1, GROUP B,C,D
Operating Temperature (Actuator): -40º to 85º C
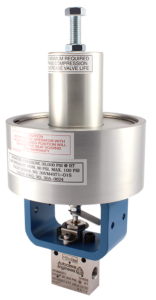
Features: Parker Autoclave Engineer’s valves are available with diaphragm or piston type actuators. Six sizes of air actuators (light, heavy light, medium, heavy duty or extra heavy, single and double stage) are offered to meet the service requirements of Parker Autoclave Engineer’s Low, Medium and High Pressure valves. Both air-to-open (normally closed) and air-to-close (normally open) designs are included in the product line. Optional air to open and close are available upon request.
Air Operator
• Maximum allowable working pressure: 100 psi (6.89 bar)
• Allowable diaphragm temperature range: -40°F to 200°F (-40°C to 93°C)
• Area of diaphragm: Light duty – 4.9 sq. in (31.6 sq. cm), Medium duty – 19.6 sq. in (126.5 sq. cm), Heavy duty – 45.66 sq. in (294.58 sq. cm)
• Approximate air usage/cycle @ 100 psi (6.89 bar): Light duty – .007 SCF (.00019 SCM), Medium duty – .07 SCF (.0019 SCM), Heavy duty – .2 SCF (.0056 SCM)
Sour + Severe Service Valves
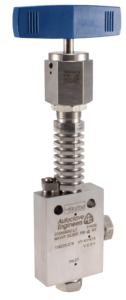
Features: Parker Autoclave Engineers has two different styles of valves for extreme temperature. Standard valves can be supplied with packing for operation from -100°F (-73°C) to 800°F (427°C), or with the addition of an extended packing housing for operation from -423°F (-252°C) to 1200°F (649°C). The extended packing housing provides the means of removing the packing from the extreme temperature medium. Machined grooves on the housing act as a heatsink to remove heat or cold. The second, which is economically priced, is a modified standard designed for the power industry. It operates to 1200°F (649°C) with graphite packing and no extended packing housing.
Extreme Temperature Valve Features:
• The extreme temperature option can be ordered on low, medium, high, micro-metering and other valve series.
• Reliable long life operation with extended stuffing box at very high and low temperatures.
• Design available for operation to 1200°F (649°C) without extended packing housing.
• Available with a variety of tubing connections and orifice sizes.
• Non-rotating stem.
• Wide range of material options
• Adjustable packing below threads.
• Metal to metal seating.
• Anti-extrusion back-up rings.
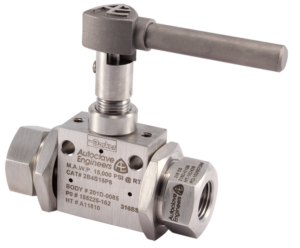
Features: Parker Autoclave Engineers subsea ball valves have been designed to fulfill the ever growing demand in the petroleum industry as well as the need for externally pressurized components in other markets. Utilizing the same design technology as the standard ball valve, the subsea design incorporates the necessary design alterations to provide a reliable externally pressurized valve for the subsea industry. With the availability of fittings, tubing, and related equipment our ball valves can provide all your needs on high-pressure applications above or below the surface.
• One-piece, trunnion mounted style, stem design eliminates shear failure found in two-piece designs.
• Re-torqueable seat glands for longer seat life.
• PEEK seats which offer excellent resistance to chemicals, heat, and wear/abrasion.
• Full-port flow path minimizes pressure drop.
• 316 cold worked stainless steel construction.
• Buna-N o-ring standard 250°F (121°C) max.
• Low friction pressure assisted graphite filled PTFE stem seal increases cycle life.
• Wide selection of tube and pipe end fittings available.
• Available to NACE MR-01-75.
• Optional wetted materials.
• Available in a number of flow configurations and port sizes.
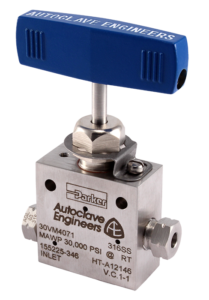
Features: Parker Autoclave Engineers offers a complete series of high pressure valves and fittings for wellhead christmas trees. Parker Autoclave Engineers components are designed and manufactured to meet or exceed API and other applicable specifications for wellhead equipment, as well as Parker Autoclave Engineers’ own exacting standards for safety, reliability and service life under high pressure operation. Parker Autoclave Engineers “SOG” components meet or exceed all requirements of NACE MR0175-2002.
Pressure/Temperature Ratings: Valves and fittings for standard service are rated for working pressure up to 60,000 psi (4137 bar) at 100°F (38°C). Type SOG components are rated up to 30,000 psi (2068 bar) at 100°F (38°C). Sizes: Parker Autoclave Engineers’ type SOG valves and fittings are supplied with standard API test and gauge connections (Parker Autoclave Engineers’ F562C).
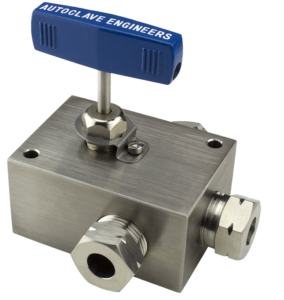
Features: Parker Autoclave Engineers’ Wellhead Gauge valves are designed for reliable shut-off service at a maximum working pressure of 30,000 psi (2068 bar). The Wellhead Gauge and Bleed Valves are standard in 316 stainless steel material. Special materials available on request.
Gauge Valve Features:
• One inlet, three outlet ports
• Metal-to-metal bubble tight shut-off
• Packing below stem threads
• Two piece non-rotating stem on standard valves
Bleed Valve Features:
• One piece hex construction allows easy installation
• Vent port tapped for plumbing to safe area
• Tee handle for easy operation
• Positive blow out prevention on stem
• 1/8” NPT outlet connection
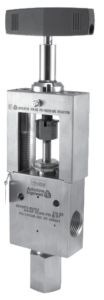
Features: Parker Autoclave Engineers’ yoke valves are extra heavy duty, plant grade instrument valves for industrial and severe service applications. Yoke valves feature low closing torque for ease of operation and are designed for use with Parker Autoclave Engineers medium and high pressure tubing and fittings.
Yoke Valve Features:
• Tubing sizes from 9/16” to 1”.
• Rising stem/barstock body design.
• Non-rotating stem prevents stem/seat galling.
• Metal-to-metal seating achieves bubble-tight shutoff, longer stem/seat life in abrasive flow, greater durability for repeated on/off cycles and excellent corrosion resistance.
Needle Valves Pressures to 50,000 psi (3447 bar)
Y Series Yoke
• PTFE encapsulated packing provides dependable stem and body sealing.
• Stem sleeve and packing gland materials have been selected to achieve extended thread
cycle life and reduced handle torque.
• Choice of Vee or Regulating stem tips.
• Available in two body patterns.
• Optional materials for cryogenic and other applications.
Subsea Valves
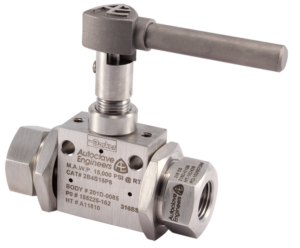
Features: Parker Autoclave Engineers subsea ball valves have been designed to fulfill the ever growing demand in the petroleum industry as well as the need for externally pressurized components in other markets. Utilizing the same design technology as the standard ball valve, the subsea design incorporates the necessary design alterations to provide a reliable externally pressurized valve for the subsea industry. With the availability of fittings, tubing, and related equipment our ball valves can provide all your needs on high-pressure applications above or below the surface.
• One-piece, trunnion mounted style, stem design eliminates shear failure found in two-piece designs.
• Re-torqueable seat glands for longer seat life.
• PEEK seats which offer excellent resistance to chemicals, heat, and wear/abrasion.
• Full-port flow path minimizes pressure drop.
• 316 cold worked stainless steel construction.
• Buna-N o-ring standard 250°F (121°C) max.
• Low friction pressure assisted graphite filled PTFE stem seal increases cycle life.
• Wide selection of tube and pipe end fittings available.
• Available to NACE MR-01-75.
• Optional wetted materials.
• Available in a number of flow configurations and port sizes.
Valve Actuators
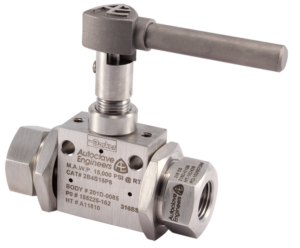
Features: Parker Autoclave Engineers subsea ball valves have been designed to fulfill the ever growing demand in the petroleum industry as well as the need for externally pressurized components in other markets. Utilizing the same design technology as the standard ball valve, the subsea design incorporates the necessary design alterations to provide a reliable externally pressurized valve for the subsea industry. With the availability of fittings, tubing, and related equipment our ball valves can provide all your needs on high-pressure applications above or below the surface.
• One-piece, trunnion mounted style, stem design eliminates shear failure found in two-piece designs.
• Re-torqueable seat glands for longer seat life.
• PEEK seats which offer excellent resistance to chemicals, heat, and wear/abrasion.
• Full-port flow path minimizes pressure drop.
• 316 cold worked stainless steel construction.
• Buna-N o-ring standard 250°F (121°C) max.
• Low friction pressure assisted graphite filled PTFE stem seal increases cycle life.
• Wide selection of tube and pipe end fittings available.
• Available to NACE MR-01-75.
• Optional wetted materials.
• Available in a number of flow configurations and port sizes.
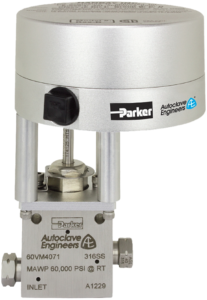
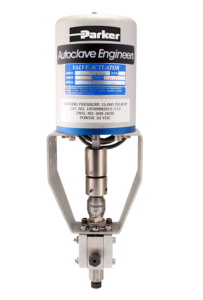
Features: Parker Autoclave Engineers has a flow control valve to remotely control process flow at high pressure for vital component to processing operations. Parker Autoclave Engineers’ control valve utilizes their standard Micro-metering valve coupled to an electric actuator. The combination of these two precision, high quality components, provide a superior low flow control valve for use with liquids and gases.
Electric Flow Control Valve Features:
• Sizes 1/8″, 1/4″ and 3/8″
• Cv: 0.004
• Precise, accurate control
• Temperatures: -100°F to +600°F
• End connections: low pressure and high pressure Autoclave
• Materials: 316 SS, special materials available
• Controller Enclosure Rating: IP65 Weatherproof
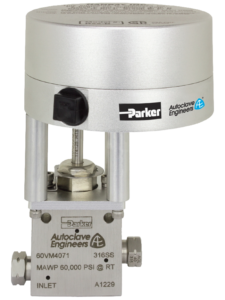
Features: The Parker Autoclave Engineers Explosion Proof Electric Flow Control valves are designed to operate up to 60,000 psi depending on the model number. The valves are “fail-as-is” meaning the valve maintains its last position on signal or power failure.
Electrical Power
Power Required: 24 VDC/72 Watt Maximum
Input Impedance: 250 Ohms (4-20 mA input)
Environmental
Atmosphere: NEC CLASS I, DIV 1, GROUP B,C,D
Operating Temperature (Actuator): -40º to 85º C
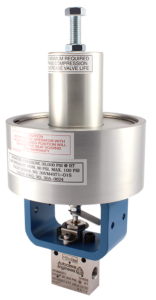
Features: Parker Autoclave Engineer’s valves are available with diaphragm or piston type actuators. Six sizes of air actuators (light, heavy light, medium, heavy duty or extra heavy, single and double stage) are offered to meet the service requirements of Parker Autoclave Engineer’s Low, Medium and High Pressure valves. Both air-to-open (normally closed) and air-to-close (normally open) designs are included in the product line. Optional air to open and close are available upon request.
Air Operator
• Maximum allowable working pressure: 100 psi (6.89 bar)
• Allowable diaphragm temperature range: -40°F to 200°F (-40°C to 93°C)
• Area of diaphragm: Light duty – 4.9 sq. in (31.6 sq. cm), Medium duty – 19.6 sq. in (126.5 sq. cm), Heavy duty – 45.66 sq. in (294.58 sq. cm)
• Approximate air usage/cycle @ 100 psi (6.89 bar): Light duty – .007 SCF (.00019 SCM), Medium duty – .07 SCF (.0019 SCM), Heavy duty – .2 SCF (.0056 SCM)